
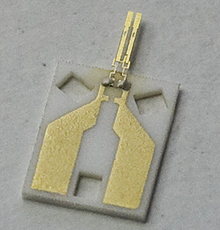
nc-AFM experiments at the atomic scale usually demand well defined environments, such as ultrahigh vacuum (UHV) and low temperatures (LT). Recent achievements of this force spectroscopy method manifest in the identification of the chemical identity of single atoms in an alloy or the measurement of the force applied during the controlled manipulation of molecules or atoms on a surface. Furthermore, the non-contact AFM (nc-AFM) technique has the capability of quantifying the interaction forces acting between the probing tip and the sample site with atomic precision. We further found significant discrepancies between experimental calibration values and predictions from the shifted beam formula, which are related to a large variance in tip misalignment during the tuning fork assembling process.Ītomic force microscopy (AFM) allows the imaging of surfaces with true atomic resolution and the resolution of intra-molecular structures of molecules. The simulations show quantitative agreement with the beam formula if the beam origin is shifted to the position of zero stress onset inside the tuning fork base and torsional effects are also included. These simulations provide a detailed view of the strain/stress distribution inside the tuning fork. In order to understand this discrepancy the complete sensor set-up has been digitally rebuilt and analyzed by using finite element method simulations. The results show a significant deviation from values calculated with the beam formula. In this study a new and easily applicable setup has been used to determine the static spring constant at several positions along the prong of the tuning fork. doi: 10.1109/ tuning forks are being increasingly employed as sensors in non-contact atomic force microscopy especially in the “qPlus” design. Three-dimensional analysis of scattering losses due to sidewall roughness in microphotonic waveguides. Hydrogen annealing effect on DC and low-frequency noise characteristics in CMOS FinFETs. Lee J.S., Choi Y.K., Ha D., Balasubramanian S., King T.J., Bokor J. Impact of sidewall passivation and channel composition on InxGa1-x As FinFET performance. Thathachary A.V., Lavallee G., Cantoro M., Bhuwalka K.K., Heo Y.C., Maeda S., Datta S. Optimization of dry etching parameters for fabrication of polysilicon waveguides with smooth sidewall using a capacitively coupled plasma reactor. Analysis of sidewall quality in through-wafer deep reactive-ion etching. Pike W., Karl W., Kumar S., Vijendran S., Semple T. In experiments, sidewalls of a micro-electro-mechanical system (MEMS) structure fabricated by deep reactive ion etching process and a standard step grating are scanned and the sidewall roughness, line edge roughness and sidewall angles are measured.Ītomic force microscopy cantilever quartz tuning fork sidewall. Owing to its unique configuration, the tip of the sensor can detect sidewall surface orthogonally during imaging, which reduces lateral friction. The attached lightweight cantilever allows high-sensitivity force detection (7.4% Q factor reduction) and sidewall imaging with high lateral resolution. A self sensing and actuating force sensor is fabricated by microassembling a commercial AFM cantilever (tip apex radius ≤10 nm) to a QTF. We report an AFM sidewall imaging method with a quartz tuning fork (QTF) force sensor.
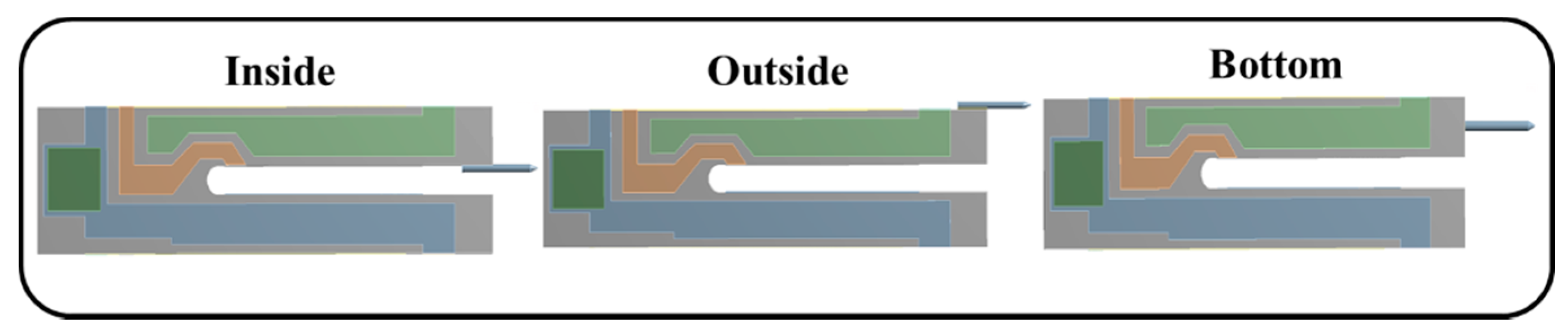
Atomic force microscopy (AFM) is an emerging technique for sidewall scanning and roughness measurement due to its high resolution, three-dimensional imaging capability and high accuracy. Sidewall roughness measurement is becoming increasingly important in the micro-electromechanical systems and nanoelectronics devices.
